Posts
Showing posts from January, 2014

Posted by
Derek Olson (Oldwolf)
After The War
- Get link
- X
- Other Apps
Posted by
Derek Olson (Oldwolf)
#SSBO or Shop Stool Build Off - Roubo Edition.
- Get link
- X
- Other Apps
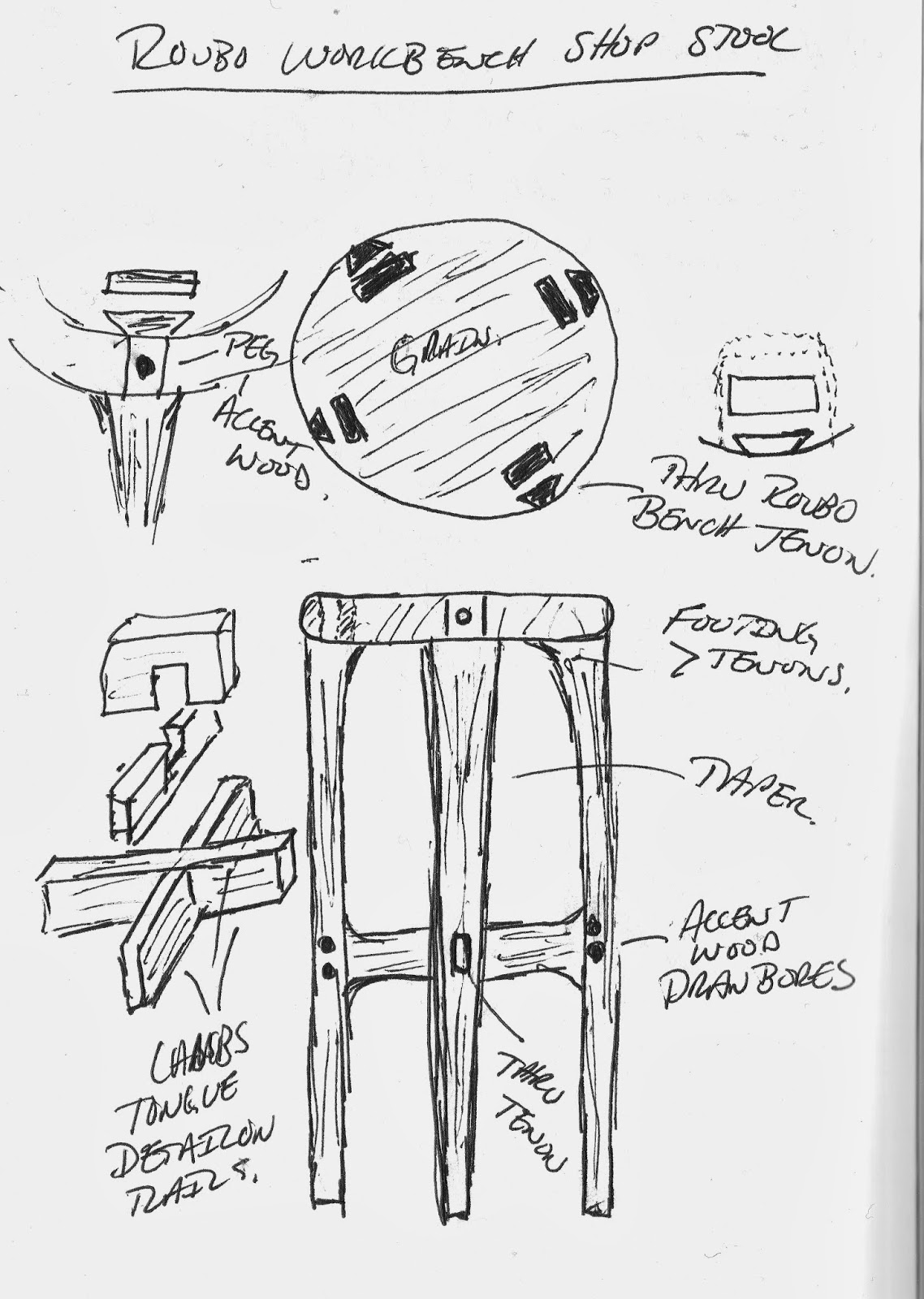
Posted by
Derek Olson (Oldwolf)
Refining Ideas.
- Get link
- X
- Other Apps

Posted by
Derek Olson (Oldwolf)
Pick Your Seat.
- Get link
- X
- Other Apps
Posted by
Derek Olson (Oldwolf)
Shop Stool Design.
- Get link
- X
- Other Apps