Posts
Showing posts from 2017
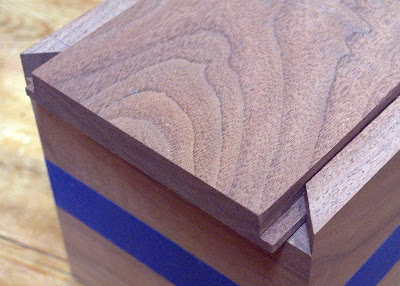
Posted by
Derek Olson (Oldwolf)
Work With Your Hands And Think On Your Feet,
- Get link
- X
- Other Apps
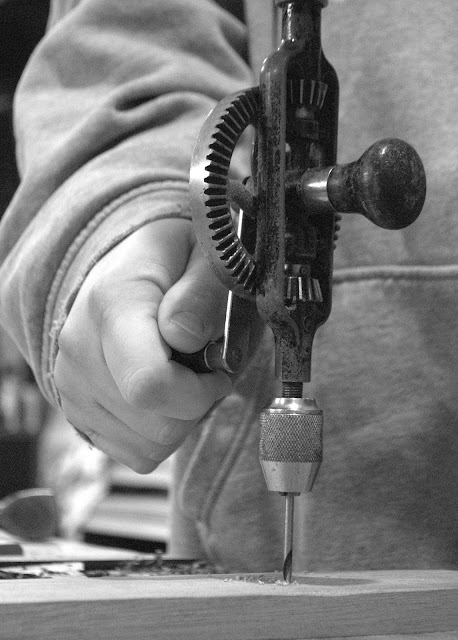
Posted by
Derek Olson (Oldwolf)
From Chaos With Love.
- Get link
- X
- Other Apps
Posted by
Derek Olson (Oldwolf)
Mitered Corners
- Get link
- X
- Other Apps

Posted by
Derek Olson (Oldwolf)
Breaking Down Odd Stock
- Get link
- X
- Other Apps

Posted by
Derek Olson (Oldwolf)
Human Touch.
- Get link
- X
- Other Apps
Posted by
Derek Olson (Oldwolf)
Check Another Bucket List Box
- Get link
- X
- Other Apps
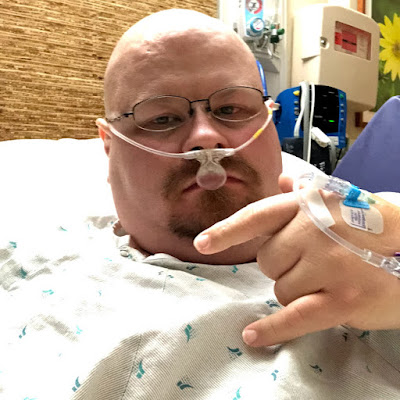
Posted by
Derek Olson (Oldwolf)
Thank You!
- Get link
- X
- Other Apps
Posted by
Derek Olson (Oldwolf)
Soon With Less.
- Get link
- X
- Other Apps

Posted by
Derek Olson (Oldwolf)
Moon Sister Pipe
- Get link
- X
- Other Apps